Generally, concrete repair materials must be compatible with the original structure. This ensures that the repaired section will continue to weather in a similar manner as its parent concrete (which typically reverts to a darker color after cleaning).
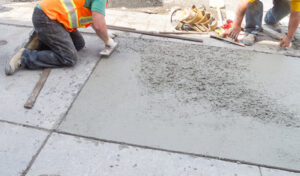
Mechanical bonding is often necessary where steel cramps or ties are inserted into concrete repairs. A scratch coat, which is a wet coating, can be used to improve the mechanical bond of repair materials with existing concrete. Visit https://www.concreterepaireauclaire.com/ to learn more.
Concrete cracks can detract from the aesthetics of a building, and if they aren’t repaired they can lead to further damage, structural failure and potential safety hazards. However, a repair must be made with consideration for the existing structure and the environment it will be placed in. It must also be made to last.
A good repair begins with figuring out what caused the crack and eliminating any additional problems. Then you can choose the best method to repair it.
For small to medium-sized cracks, a standard crack filler will work. A latex-based product can be applied with a caulking tube or from a bucket, and it cleans up easily and quickly. Polyurethane-based products are more durable, offer superior bonding and have a long service life.
Before applying the crack filler, a thin layer of bonding adhesive should be applied to both sides of the crack. This improves adhesion and reduces the risk of future cracking. The crack filler should then be force- and tamper-applied into the crack, using enough pressure to compact it. This will usually create a void that can be filled with concrete.
For larger cracks, a different method is required to prevent them from re-opening and expanding. This is called crack stitching. The process involves drilling a hole down the length of the crack and then plugging it with grout or epoxy. This creates a “grout key” that locks the crack and prevents further movement.
If the crack is in a load-bearing section of a concrete slab, it may be necessary to add rebar for additional strength. If the corrosion of rebar is a concern, it’s important to choose a repair method that will adequately protect the steel from future attack. Impressed current cathodic protection (ICCP) is an excellent choice because it doesn’t require the removal of concrete and it provides long-term corrosion control.
For extensive cracking, heaving and spalling, or sections of concrete that have been weakened by chloride contamination or aggressive soil conditions, alternative methods should be considered. Drilling and plugging, crack stitching or concrete injection are all methods that can be effective in repairing these more severe problems.
Sealing Cracks
Concrete is hard and durable, but it can crack over time. There are a number of methods for repairing and sealing cracks in concrete. Some methods are quicker and more affordable than others. The method you choose will depend on the size of the crack and whether it is dormant or active. It is important to fix the cause of the crack before it gets worse.
The first step in repairing concrete is to identify and document the problem. This should include taking before and after photos, ensuring the surface preparation is acceptable including observing cleanliness and surface amplitude or direct tension testing, material testing by a qualified testing agency and sounding the finished repair to detect voids or lack of bonding.
Before you start repairing concrete, you should clean the crack. This will help the filler or sealant adhere to the existing concrete. It is also a good idea to widen the cracks to the full depth of the concrete to help with long-term durability.
Once the cracks are clean, you can begin by chiseling away any loose material from the sides of the crack. This will give the masonry crack filler something to stick to. If the crack is very narrow, you may want to stuff foam backer rod into the crack to help support it. This is especially true for concrete that has been subjected to a lot of traffic or vibration.
When applying the repair product, it is important to follow the manufacturer’s directions for application. If possible, apply the bonding agent directly to the existing concrete rather than mixing it into the concrete. Then apply the crack filler or masonry crack sealant.
Some products claim to have high early strength gains, which can be helpful in getting the concrete to a stable state faster. However, this will likely come at the cost of a reduced long-term service life for the repair.
For very thin cracks, you can use epoxy injection. This is a fast and inexpensive method that can be used to repair leaks or to fill small to medium sized cracks.
Repairing Leaks
If you have a water leak in concrete, it’s important to fix it as soon as possible to prevent further damage. Moisture leaking through concrete walls and foundations can lead to structural failure as well as encourage the growth of mould, which may also threaten human health.
The first step in repairing a leak is to expose the source of the leak. This usually involves breaking up a small section of concrete with a jack-hammer to reveal the pipe. Then the pipe must be removed, cleaned and inspected to determine the cause of the leak.
Professionals use various tools to pinpoint the location of a slab leak in order to repair it effectively. They can trace the path of the copper line with tracing equipment, listen for the sound of the leak in order to locate it under the dirt and concrete, and use infrared thermometers to identify hot spots where a plumbing leak is located.
Once the leak is located, a hole is drilled through the slab in order to access the damaged line. The line is then removed and replaced with a new one. The hole is then patched and the surface is smoothed and finished in order to ensure a proper bond with the new concrete.
There are many different types of materials used for repairing leaks in concrete, including foams and quick-setting cement-based repair mortars. The material selected will usually have properties similar to the parent concrete in terms of modulus of elasticity, freeze-thaw resistance and scaling resistance. The surface of the repaired concrete should also be free of deleterious contaminants that will inhibit bonding.
For large parking decks or other projects that require a lot of concrete, pre-blended ready mix concrete delivered directly from a concrete plant is an economical choice. For smaller repairs, bagged concrete repair products are available that can be mixed on-site with water to form a concrete mix. Once the repair area is prepared by removing the old concrete and cleaning, backfill materials are added and compacted to achieve an optimum density. Depending on the nature of the repair and the application, it is often necessary to add waterproofing additives in order to prevent moisture intrusion.
Repairing Slabs
Concrete slabs serve a variety of purposes, including driveways, sidewalks, patios and garage floors. They need to be able to support a considerable amount of weight, especially when the surface is exposed to the elements and traffic. Slab cracks and damage are common, and they should be repaired promptly to minimize water intrusion, safety hazards and potential damage to adjacent structures.
Slab repair can include the filling and bonding of small areas with a concrete patch material, removing and replacing deteriorated concrete slabs, and repairing cold joints at the slab-to-driveway or slab-to-garage floor connections. Slab repair may also involve reinforcing the entire slab with new steel bars, depending on the extent of the problem and the anticipated use of the slab.
If the slab has a minor defect such as cracks that do not penetrate to the steel reinforcement, surface filling is an economical and quick solution. A concrete patch product can be poured over the surface and left to set. A sealer can be applied afterwards to help protect the patch and extend the life of the repair.
For larger repairs, a concrete mix should be designed with less water than the original to reduce shrinkage and improve strength development. The addition of a bond coat made of equal parts portland cement and sand will help ensure the new concrete adheres to the existing slab.
Using saw cuts to define the perimeter of the concrete patch will help to avoid the formation of dying shrinkage cracks in the repair material, which can affect long-term durability. Ideally, the concrete patch should be rectangular or square in shape, to make it easier to place and compact.
A common mistake contractors make when working on slab repair is to apply a thick concrete mix over the area and then use a float to smooth it. The resulting concrete is often too stiff to bond to the existing concrete, and it will crack and crumble.
A more effective approach is to use a low slump, high-density foam such as PolyLevel to fill the void and lift the concrete back to its original position. This technique is noninvasive, leaves no injection holes, and doesn’t retain moisture that can pull the concrete down.